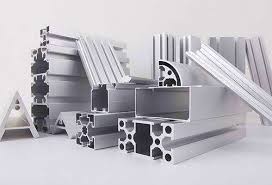
In the world of manufacturing, materials play a crucial role in determining the efficiency, durability, and performance of a product. One material that has revolutionized various industries is aluminum, particularly in the form of large extruded aluminum. This article will explore the significant benefits of large extruded aluminum in modern manufacturing, highlighting its impact on industries ranging from aerospace to construction, automotive, and electronics.
What is Large Extruded Aluminum?
Before delving into the benefits, it’s essential to understand what large extruded aluminum is and how it’s produced. Extrusion is a manufacturing process that involves forcing a material through a die to create long shapes with a constant cross-section. In the case of aluminum, this process allows manufacturers to produce a variety of shapes and profiles, including rods, bars, tubes, and complex sections, all in large sizes suitable for various applications.
Large extruded aluminum refers to aluminum profiles that are larger in dimension compared to typical extrusions, often requiring specialized machinery and techniques to produce. This process can create lengths up to several meters long and profiles that can handle heavy-duty applications across multiple industries. Large extrusions are particularly beneficial in sectors that require materials with high strength, light weight, and excellent corrosion resistance.
1. Lightweight Yet Strong
One of the primary reasons large extruded aluminum is preferred in manufacturing is its excellent strength-to-weight ratio. Aluminum, when compared to other metals like steel or copper, is lightweight while still maintaining substantial strength. This makes it an ideal choice for industries where weight reduction is critical without compromising on durability.
In the aerospace industry, for example, large extruded aluminum is extensively used in aircraft frames, wings, and fuselages. The lightweight nature of aluminum contributes to fuel efficiency by reducing the overall weight of the aircraft. This results in lower operating costs and a reduced carbon footprint, making aluminum a critical material for sustainable aviation.
Similarly, in the automotive sector, large extruded aluminum is used in manufacturing car bodies and structural components. The use of aluminum helps reduce the overall weight of vehicles, which in turn improves fuel efficiency and performance. With increasing regulations around fuel consumption and emissions, manufacturers are turning to lightweight materials like aluminum to meet these stringent requirements.
2. Corrosion Resistance and Durability
Another significant benefit of large extruded aluminum is its resistance to corrosion. Aluminum naturally forms a protective oxide layer on its surface when exposed to air, preventing further oxidation and rust. This makes aluminum highly durable and well-suited for environments where exposure to moisture, chemicals, or other harsh elements is common.
For example, in the construction industry, large extruded aluminum is often used for window frames, curtain walls, and architectural facades. Aluminum’s corrosion resistance ensures that these components remain structurally sound and aesthetically pleasing for extended periods, even when exposed to the elements. In coastal regions where saltwater corrosion is a concern, aluminum’s resistance to corrosion makes it a preferred choice over other materials like steel.
Additionally, the durability of large extruded aluminum means it can withstand mechanical stresses, temperature fluctuations, and other harsh conditions. This makes it an excellent choice for marine environments, where materials are often exposed to saltwater and extreme weather conditions.
3. Versatility and Customization
Large extruded aluminum offers unparalleled versatility, making it suitable for a wide range of applications. The extrusion process allows for customization in terms of size, shape, and design, meaning that manufacturers can produce aluminum profiles that meet specific requirements for different projects.
In the electronics industry, large extruded aluminum is commonly used for heat sinks. These heat sinks are designed to dissipate heat away from sensitive electronic components like processors, preventing overheating and ensuring the longevity of the device. The ability to create complex profiles with fine details enables manufacturers to design highly efficient heat sinks that can be tailored to the exact specifications of the electronic device.
Moreover, aluminum extrusions can be easily modified through post-extrusion processes such as anodizing, painting, or coating, which further enhance their appearance and performance. Anodized aluminum, for instance, has an additional layer of protection that increases its resistance to corrosion and wear while providing an aesthetically pleasing finish.
4. Sustainability and Eco-Friendliness
Sustainability is a significant concern in modern manufacturing, and large extruded aluminum plays a crucial role in helping companies reduce their environmental impact. Aluminum is highly recyclable, and the extrusion process itself is energy-efficient compared to other methods of shaping metals.
Recycling aluminum requires only about 5% of the energy needed to produce new aluminum from raw materials, making it one of the most environmentally friendly materials available. This closed-loop recycling process reduces the demand for raw bauxite and minimizes the carbon footprint of aluminum production.
The use of large extruded aluminum in manufacturing contributes to sustainability in several ways. For example, aluminum components in automobiles and aircraft can be recycled at the end of their life cycle, reducing the need for new materials. In the construction industry, aluminum frames and panels can be reused or repurposed in new buildings, further minimizing waste and the environmental impact.
In addition, the lightweight nature of aluminum reduces energy consumption in transportation, whether it’s in the form of vehicles, ships, or aircraft. By reducing the weight of transportation systems, fuel consumption is minimized, leading to lower greenhouse gas emissions and a smaller carbon footprint.
5. Cost-Effectiveness
While aluminum is often considered a premium material, large extruded aluminum can be cost-effective when compared to other materials with similar performance characteristics. Aluminum’s abundance and recyclability help keep costs lower than other metals like titanium, while still offering superior strength and performance.
In industries like construction, where large quantities of material are needed for structural elements, the cost-effectiveness of aluminum can be a significant advantage. The ability to produce large extrusions with minimal waste ensures that manufacturers can keep production costs down, which is particularly important in competitive markets.
Furthermore, aluminum’s ease of machining and fabrication means that manufacturers can quickly and efficiently create custom parts without the need for expensive tooling or complex processes. This reduces lead times and helps businesses meet tight deadlines without compromising on quality.
6. Ease of Fabrication and Joining
Large extruded aluminum can be easily fabricated and joined using a variety of techniques, including welding, riveting, bolting, and adhesive bonding. This flexibility in joining methods allows manufacturers to choose the most appropriate technique for each specific application, depending on factors like strength, aesthetic preferences, and ease of assembly.
In the automotive industry, for example, large extruded aluminum profiles are often used for frame construction, where precision and strength are crucial. The ability to weld or bolt aluminum parts together ensures a strong and reliable structure. Similarly, in the construction industry, aluminum framing systems can be easily assembled on-site using simple joining techniques, reducing the need for complex tools and minimizing installation time.
Additionally, the low thermal conductivity of aluminum means that it is easier to handle during the welding process, reducing the risk of distortion and warping. This makes aluminum a popular choice for precision manufacturing, where tight tolerances are required.
7. Applications Across Industries
Large extruded aluminum is used in a diverse range of industries due to its unique properties. The following are some of the most common applications:
Aerospace: Aircraft manufacturers rely heavily on large extruded aluminum for creating lightweight, high-strength components like wings, fuselages, and landing gears. The material’s ability to withstand extreme temperatures and pressures makes it indispensable in the aerospace industry.
Automotive: In the automotive sector, large extruded aluminum is used in the production of vehicle bodies, structural frames, and chassis components. The material’s lightweight nature helps reduce vehicle weight, improving fuel efficiency and safety.
Construction: Aluminum extrusions are commonly used in building materials such as window frames, doors, and curtain walls. The material’s corrosion resistance and aesthetic appeal make it ideal for both commercial and residential construction.
Electronics: Large extruded aluminum profiles are used for heat dissipation in electronic devices. Custom-designed heat sinks ensure that electronic components stay cool, preventing overheating and extending the life of the device.
Marine: In the marine industry, large extruded aluminum is used for boat hulls, masts, and other structural components. Aluminum’s resistance to saltwater corrosion makes it an ideal choice for maritime applications.
Conclusion
Large extruded aluminum has become an essential material in modern manufacturing due to its unique combination of strength, lightweight properties, corrosion resistance, and versatility. From aerospace to automotive, construction, and electronics, aluminum extrusions play a critical role in shaping the products we use every day.
The material’s sustainability, cost-effectiveness, and ease of fabrication ensure that it will continue to be a preferred choice in a variety of industries for years to come. As industries continue to demand higher performance and greater environmental responsibility, large extruded aluminum will remain a cornerstone of modern manufacturing, offering innovative solutions for the challenges of the future.